In the section of “Safety and Disaster Prevention” of our Responsible Care (RC) policy, we aim to achieve zero accidents and disasters based on the principle that “ everything begins with safety. In addition, we promote security management of facilities in compliance with related laws and regulations, and maintain a crisis management system in case of emergency.
Osaka Soda is taking action for security and disaster prevention, including establishing a basic policy for security management implemented at each business site. Furthermore, Osaka Soda has built a security management system for security, facilities, and operation to be implemented at each business site under the purview of the Group-wide and individual business site RC committees. In addition, Osaka Soda strives to prevent serious accidents with both soft and hard measures. These include training operators to improve their field capabilities and operating techniques, and carrying out systematic maintenance management for facilities (planned and preventive maintenance)
Security Management Policy
(Mizushima Plant / Okayama Plant)
- Strive for zero accidents and zero injuries based on the concept that safety is the starting point for all activities
- Strictly follow the crisis management system during emergency situations
- Promote security management of facilities and strive to improve security capabilities
- Maintain and continually improve the security management system
- Uphold specific requirements set forth at the plant
- Establish security management targets based on this policy and strive to achieve them
- Review security management targets at least once a year at the plant RC Committee
- Disseminate this policy to all plant workers for greater understanding and to ensure proper implementation, upkeep, and improvement
Mizushima Plant and Okayama Plant have established and are operating a security management system based on the Security Management Policy. Both plants, which are certified as approved sites of business under the High Pressure Gas Safety Act, operat a security management system and also undergo security certification inspections and internal audits in order to improve the security management level.
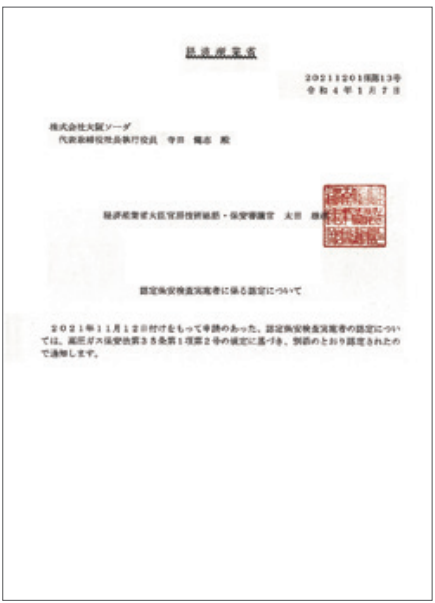
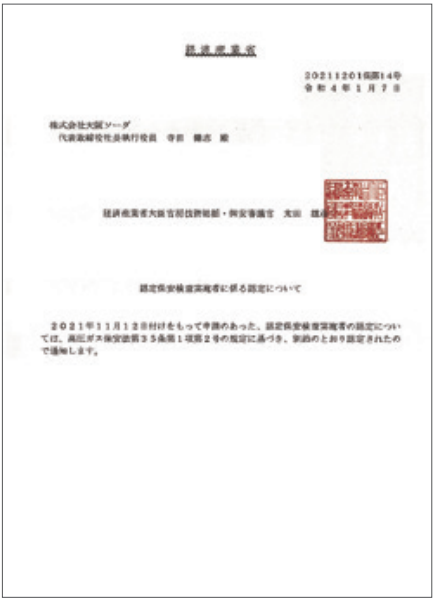
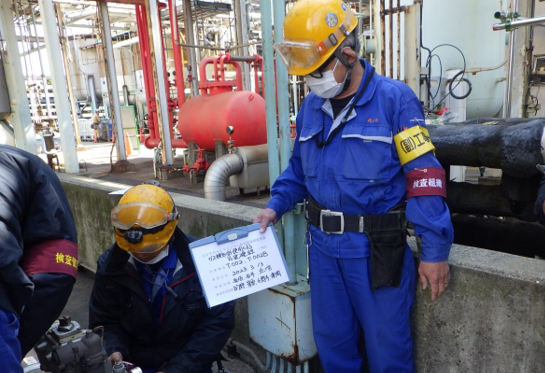
Security certification inspections
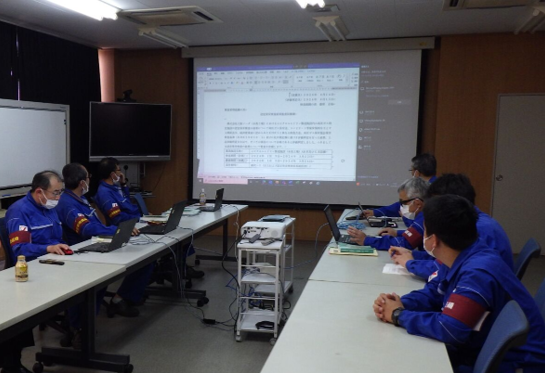
A facility management system has been introduced and put into operation for systematic facility management. In addition, to encourage autonomous maintenance activities, Osaka Soda helps personnel gain qualification for the Autonomous Maintenance Certificate. In fiscal 2023, seven employees qualified for the Autonomous Maintenance Certificate (level 1).
In order to promote facility management (zero serious accidents), we undertook security management at the Mizushima Plant and Okayama Plant based on the approved high-pressure-gas certified site of a business system. As a result, there were zero serious accidents (class A accidents) and zero class A (minor) accidents at the plants in fiscal 2023. We are continuing to reinforce our security management system.
HAZOP and other methods are used to identify hazard sources, conduct risk assessments, and systematically implement risk mitigation countermeasures according to the magnitude of risk. In fiscal 2023, we proceeded with risk mitigation initiatives with respect to identified sources of hazards as a response using KY, RA, SA, HAZOP and others to reduce risks and identified sources of hazards.
In the event of a major earthquake or other disaster or emergency, our safety confirmation system simultaneously sends e-mails and other communications to employees' registered contact information. Employees at business sites in the area of an earthquake of seismic intensity 5 (on the Shindo scale) or higher are automatically sent safety confirmation messages.
Each site participated in local disaster prevention drills. In addition, we conduct comprehensive disaster training in anticipation of large-scale earthquakes etc., as well as reporting and communication drills, oil spill response team dispatch drills, high-pressure gas disaster prevention drills, etc., at each plant and workplace. We will continue to improve our response capabilities in the case of a major earthquake or other disaster.
- 拡大
- Joint Disaster Prevention Training
(Matsuyama Plant)
As part of its safety and disaster prevention activities, the Group maintains a crisis management system necessary to prevent accidents and disasters, and conducts various drills to prepare for disasters, as well as to ensure the maintenance of plant facilities and the thorough management of hazardous materials, high-pressure gas, and toxic substances handled.
The Mizushima and Matsuyama plants have formed a joint disaster prevention organization as stipulated by the Act on the Prevention of Disaster in Petroleum Industrial Complexes and Other Petroleum Facilities, and are engaged in prompt and appropriate firefighting activities.
In preparation for a major earthquake, which is forecast to occur in the near future, Osaka Soda has formulated a Business Continuity Plan (BCP) for each manufacturing site assuming damage to production facilities at each workplace and based on forecasts for the restoration of utilities including various raw materials, water, and electricity as well as logistics. Moreover, Osaka Soda has also prepared emergency response guidelines at each site and made all employees aware of the chain of command in an emergency and the procedures for confirming safety. In fiscal 2023, we revised the BCP for earthquakes, torrential rains, and infectious diseases.