In the section on occupational health and safety in Responsible Care (RC) policy, we promote various initiatives to foster a safety culture, reduce potential hazards, strive to eliminate workplace accidents, establish a pleasant workplace environment, and maintain and promote the health of our employees.
By working to implement such measures as serious accident prevention and KY activities and regular meetings of the RC Committee (includes the Safety & Health and Process Safety & Disaster Prevention Committee), we are working to prevent lost worktime accidents with the goal of zero lost worktime accidents.
Number of Annual Lost Worktime Accidents (Year)
2019 |
2022 |
2021 |
2022 |
2023 |
|
Number of lost worktime accidents |
1 |
1 |
3 |
2 |
1 |
Frequency rate of lost worktime accidents* |
0.70 |
0.71 |
2.02 |
1.34 |
0.68 |
- Frequency rate = (No. of victims of lost worktime accidents ÷ total working hours) x 1,000,000 Frequency rate of accident victims per 1,000,000 working hours
Each plant and the Research Center foster hazard prediction (KY) trainers through external courses, which are reflected in workplace KY activities.
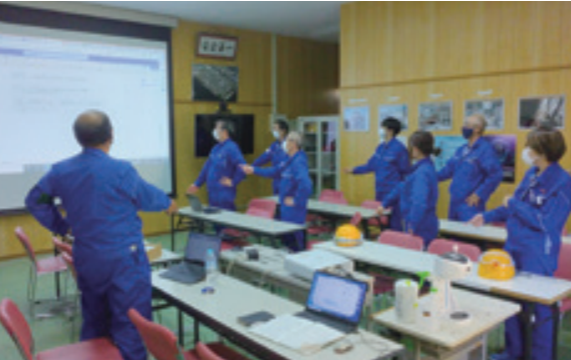
Non-technical skills (NTSs) are skills that supplement technical skills and contribute to the safe and efficient execution of work and consist of situational awareness, communication, leadership, courage to speak out, verbalizing, reflection, and overcoming the authority gradient. Osaka Soda provides NTSs education at 5 plants to prevent errors related to human factors and ensure safety.
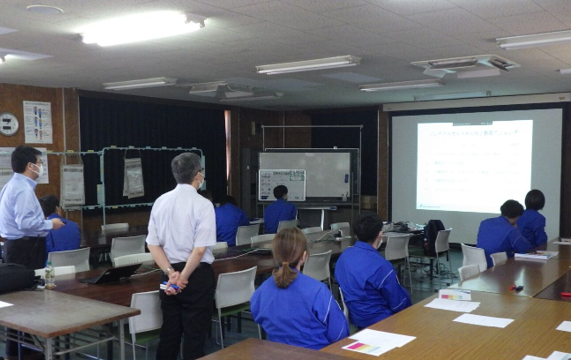
Osaka Soda is working to improve understanding of the basic principles of machinery, electricity, and instruments and skills related to such operations as maintenance by introducing training for plant engineers provided by independent organizations.
In fiscal 2023, 22 employees received the training.