In order to provide products that satisfy its customers, the Group continuously works to establish product reliability and safety and improve quality assurance levels. To this end, Osaka Soda has adopted the methods in ISO 9001, the international standard for quality management systems, and ICH-GMP (Good Manufacturing Practice Guide for Active Pharmaceutical Ingredients) for quality management.
-
We will comply with all laws and regulations and provide products and services that satisfy our customers.
-
We strive for consistent product quality and production through continuous improvement of our quality management system.
-
We will consider the environment throughout the product life cycle and provide products that can be handled safely and reliably.
-
We will accurately grasp customer needs and work to improve quality.
-
We will conduct quality assurance activities to enhance customer trust.
As part of our RC activities, Osaka Soda implements initiatives on safety and quality assurance for the chemicals and products in our business activities as well as to respond promptly to customer requirements and to prevent quality problems. Accordingly, our three main plants have ISO 9001 certification, the international standard for quality management systems. As a part of ISO activities, each site conducts a management review to check customer satisfaction levels, which are evaluated through the marketing department every six months, in our efforts to enhance customer satisfaction through continuous improvements as Osaka Soda strives to provide products that satisfy our customers.
Plant |
Date of Certification ISO9002 |
Date of Transition ISO9001 |
Certifier |
Registration Number |
Amagasaki Plant |
March 1996 |
May 2003 |
Japan Quality Assurance Organization |
JQA-1181 |
Matsuyama Plant |
October 1995 |
November 2002 |
Japan Quality Assurance Organization |
JQA-0998 |
Mizushima Plant |
June 1994 |
July 2003 |
Japan Quality Assurance Organization |
JQA-0539 |
- 拡大
- ISO Registration certificate
(Amagasaki Plant)
- 拡大
- ISO Registration certificate
(Matsuyama Plant)
- 拡大
- ISO Registration certificate
(Mizushima Plant)
Products subject to GMP, such as modified silica gel, are supplied under GMP control in accordance with our GMP policy and customer requirements, and GMP control standards are operated in accordance with ICH-GMP (Q7A: GMP Guide for API).
GMP Policies
- Maintain a high level of 5S (Seiri, Seiton, Seisou, Seiketsu, Shitsuke) and ensure that work is performed in accordance with established procedures.
- Implement manufacturing and quality control based on scientific evidence to supply products required by customers.
- Promptly obtain information related to GMP and take appropriate actions.
Our quality assurance organization is headed by the Quality Assurance Committee, which reports directly to the President. This committee manages industrial manufacturing products such as chemicals, functional chemicals, and polymers, products subject to GMP such as modified silica gel, and external products such as outsourced products, as indicated in the figure below. In addition, ISO 9001-certified plants conduct internal audits and undergo external audits, and GMP organizations conduct internal audits for continuous improvement.
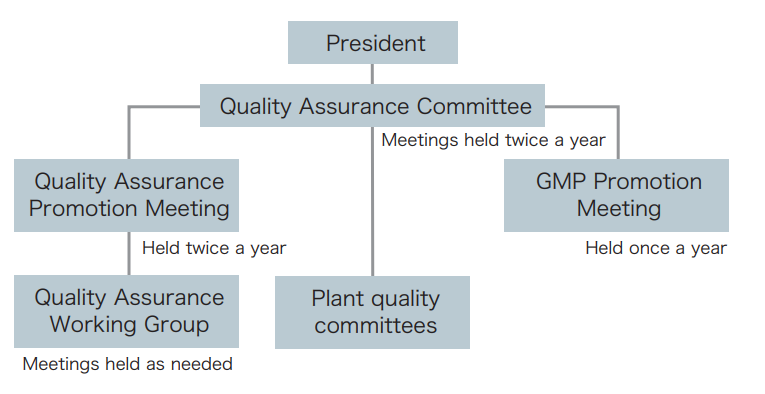
Quality audits are conducted twice a year at each plant to prevent quality incidents and ensure consistent quality. In parallel with quality audits, the quality assurance group of each plant is also involved in efforts to raise the level of quality assurance by examining quality incident case studies and providing compliance education on the importance and role of quality assurance groups. In fiscal 2023, we worked to revise the QC process schedule and rigorously enforce change management in order to curb non-conforming products, a KPI. Furthermore, we set material purchase specification sheets with suppliers and confirm that analysis figures of delivered raw materials meet the acceptance standards.
Osaka Soda operates a database in order to promptly respond to and correct quality problems such as complaints. By sharing the information in the database, Osaka Soda conducts company-wide horizontal deployment of corrective action to prevent the occurrence of similar quality problems.